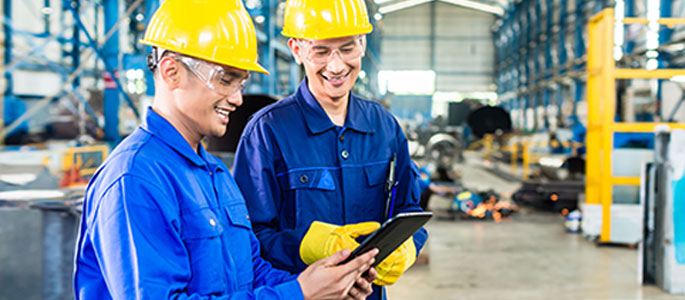
Southeast Asia has always been one of the most attractive regions for manufacturing investments. Though it had lost sheen due to the rise of Chinese manufacturing, the COVID-19 pandemic has marked a change in shift, making Southeast Asia emerge again as an alternative option due to the many advantages it offers on the geographic, economic, demographic, and regulatory fronts.
A lot of work still needs to be done though, especially in the area of supply chain realignment, and an ERP solution can come in handy. Details in the blog:
Overview
Manufacturing has been the beating heart of the Southeast Asian countries. According to a report published in the Swedish management consulting firm Business Sweden, manufacturing sector is a major driver of growth in the region, accounting for over 20% of its GDP.
As a matter of fact, manufacturing has brought about significant changes in past couple of decades in this region, particularly in countries like Singapore, Vietnam, Thailand, Philippines, Indonesia and Malaysia.
However, with emergence of China as a manufacturing powerhouse in the last decade, when it overtook the United Stated of America (USA) in 2011 to become world’s largest producer of manufactured goods, Southeast Asia lost the advantage it had.
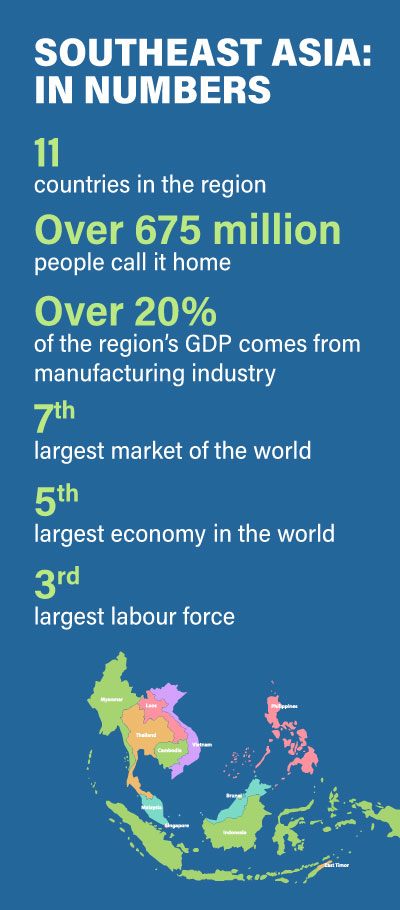
But, the tide is turning
The cold trade war between the USA and China, the Coronavirus Pandemic that hit the latter first, and then the entire world, and the increasing labour and production costs in China have engineered a rapid structural shift, making Southeast Asia the focal point of manufacturing operations, once again.
However, these are just the triggers, but what has actually facilitated this change is the conducive environment the Southeast Asian countries offer to manufacturing companies to invest in their region. The fifth-largest economy in the world in terms of GDP (combined GDP of US$3.2t in 2019), the region holds immense growth potential, and offers numerous advantages to potential investors.
Abundance of lower-skilled as well as skilled workers, significantly lower labour costs (labour costs in Indonesia, for example, are just one-fifth of the costs in China), continuously improving policies that allow ease of doing business, rapid adoption of technological advancements, investment in infrastructure & manufacturing capabilities, and incentives such as tax holidays and grants together make Southeast Asia an attractive location for companies seeking to relocate their manufacturing or supply chain hubs.
But even as these favourable factors present businesses with a great opportunity to expand their manufacturing and supply chain capabilities in the region, there remain supply chain pitfalls that the existing Southeast Asian manufacturing businesses face, and need to address in order to build resilient supply chains.
A look at those pitfalls first
Here are a few gaps that the Southeast Asian manufacturers need to plug:
– Relatively underdeveloped supply chain infrastructure
The growing interest of manufacturing companies in the region notwithstanding, the Southeast Asian supply chain infrastructure still needs to do a lot of work to meet the levels of Chinese supply chains. Products take many layers to reach the consumer, the information flow isn’t as consistent as it should be, and the existing system makes product visibility and tracking difficult.
– Third-party reliance
Some manufacturers rely heavily on third-parties, or on a narrow set of global vendors, for supply of critical components, which exposes them to risks such as regulatory compliance, and quality assurance, thus making the supply chain prone to disruptions. This pushes the case for supplier risk assessment, for analyzing the risk profile of third parties and conducting a review of their ability to meet essential supply requirements, and for more resiliency in the supply chain.
– Lack of real-time, accurate data
In the absence of a specialized supply chain management solution, manufacturers struggle to get real-time and accurate data across the supply chain, and efficiently forecast consumer demand, among other things, which affects the agility of their supply chain in the face of rapid changes.
– Absence of sustainable practices
One of the latest trends going around in the manufacturing industry dictates the manufacturers to adopt sustainability standards, with more and more consumers favouring products coming from organizations with sustainable practices. However, committing to sustainable practices comes at a cost of increased pressure on margins, forcing manufacturers to realign the supply chain so as to strike a balance between customer expectations and profits.
– Unintelligent supply chain
In the absence of intelligent and technology-driven analytical tools, manufacturers fail to gather insights around supply chain diagnostics, supplier performance, market intelligence, and risk management, among others. This is another potential trigger for supply chain disruption, and the manufacturers need to address it.
And now, at the fixes
Now, let’s take a look at how the Southeast Asian manufacturers can use an ERP software system to realign the supply chain.
– Inject traceability & trackability
An ERP software offers manufacturing businesses the ability to trace and track every single unit of a product at any time, and with it, the power to share the complete details regarding a product’s journey through the supply chain, with all the other supply chain participants. Empowered with this functionality, the Southeast Asian manufacturers can focus on building a strong, efficient and well-integrated supply chain.
– Supplier due diligence
A good ERP software system makes risk due diligence a natural part of the process for manufacturing businesses. This way, the manufacturers can identify key suppliers, evaluate their risks as well as ability to meet supply requirements of right quality standards and timeliness, and segment them based on the risk exposure. With this information at their disposal, the manufacturers can make timely and accurate business decisions, improve collaboration with the supply chain partners, and avoid sudden disruptions in supply chain by making it more resilient.
– Get real-time, accurate data
An ERP system that comes with demand forecasting as well as supply chain management functionality helps synchronize supply and demand so as to meet customer delivery expectations. It allows the manufacturing businesses to leverage data and get actionable insights, and offer advanced analytics shared throughout the supply chain. By collecting and analyzing this data, real-time reports can be generated, and organizations can make critical decisions.
– Add sustainability
An ERP system, when implemented, delivers an unprecedented level of efficiency, and agility through its advanced analytics to bring the production and distribution activities in sync in order to match demand. This streamlines the supply chain, which in turn allows the manufacturers to improve collaboration with key supply chain partners and reduce inventory lifetime miles to reduce their carbon footprint. Besides, it also helps implement lean and sustainable practices across the supply chain, and bring down waste, among other things.
– Implement intelligent practices
Recent researches reveal that more manufacturers are increasingly opting for integration of modern technologies and tools with their ERP systems, with the aim of making their supply chain intelligent, than ever before. An ERP solution equipped with the planning and predictive analytics capabilities, for example, gives the manufacturers complete picture to plan an effective response to any supply chain risk or disruption, thus offering them a competitive advantage.
Concluding thoughts
While supply chain disruptions have become a norm for manufacturers across the globe, the stage is set for Southeast Asia to become a key figure in the global supply chain. All that is required is a little bit of work on the supply chain front. Tools such as an ERP software can help the manufacturers realign the supply chain, and make it a reality. If you’re operating a manufacturing business in the region, and are looking to revolutionize your supply chain, get in touch with the ERP solution experts of BatchMaster, today!