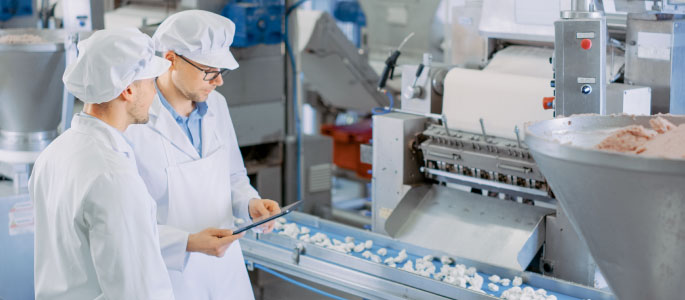
If yours is a food and beverage manufacturing organization of any type, size and scope operating in the South Asia region, reducing the cost of doing business and improving profitability should be on top of your to-do list. Are you aware a food ERP software can help you in this regard? Read this blog to find out how.
Overview
Two of the biggest objectives of any business enterprise are to reduce costs and earn profit, and most businesses fail to realize that both these things happen to be correlated. If a business can cut down the overhead and operating costs successfully, it can have more money to invest in R&D, or in offering products at a competitive price, and eventually, to make more profit.
But this is all easier said than done.
And all of it certainly can’t be achieved by working without an ERP software. Talking from a food and beverage manufacturer’s perspective, it is essential to have a food ERP software in place, so that the different costs related to the business can be managed and controlled, and profits can be enhanced.
Generally speaking, an ERP software can help the food and beverage manufacturers unlock more profits by streamlining their core operations, reducing waste, helping build lean business processes, and keeping a strict check over the different business costs.
We’ll go a bit granular to understand how the food and beverage manufacturers can actually reduce the costs and improve profits with a food ERP software.
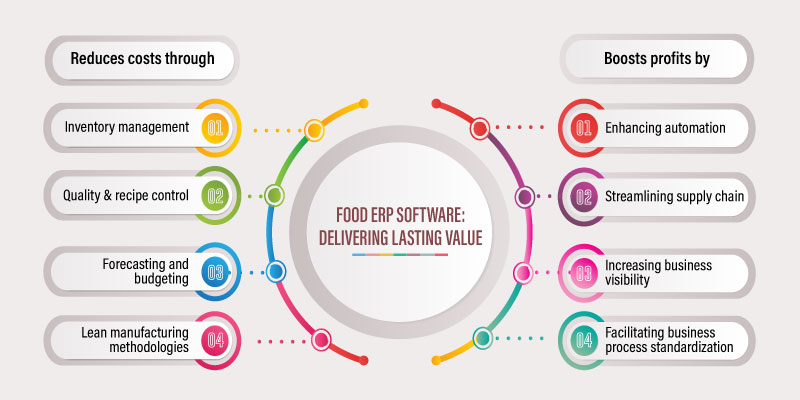
Let’s talk about reducing the costs first
– Inventory costs
There are several features in ERP for food and beverages industry that help you manage and control the different costs such as the inventory purchasing costs, and the inventory holding costs.
It is particularly important for a food and manufacturing business to have complete control over their inventory, because inventory is something that can be costly to have, to write off, and not to have in sufficient quantity. An ERP in food industry helps manufacturers manage their inventory — which often has limited shelf-life — smartly, and keep the inventory costs in check.
The dynamic business environment of current times dictates the fluctuations of material costs. But a robust ERP software for food industry automates anticipating future changes in these costs, allowing the manufacturers to take necessary preventive actions.
The demand forecasting capability of an ERP for food and beverages industry, for example, helps manufacturers bring down the purchasing costs significantly by offering valuable insights into the ideal inventory levels, and space planning, and also by allowing them the room for upfront negotiations with the suppliers on the discount.
Through its Material Requirement Planning (MRP) functionality, it can help you manage your reorder point (ROP) thresholds, telling you when to place an order based on your current inventory levels, and economic order quantity (EOQ), which determines how much to buy when placing those orders. In short, it can help you avoid having excess inventory that becomes costly and unmanageable.
– Manufacturing costs
Using an ERP software, food manufacturers can implement lean practices such as just-in-time manufacturing, and make best use of its built-in processes to capture and track all costs – material, labour, overhead, and all other costs that can help identify exactly how much it costs to manufacturer their products.
By going lean, manufacturers canplan and schedule their shop floor processes optimally, and produce just enough output to satisfy the demand, which reduces the costs associated with storage and shipping goods before sale. Also, with an effective lean workflow in place, they can also bring down the scope of errors and reworks, reduce waste, and eventually the costs that come along.
Additionally, any good ERP for food and beverages industry comes with recipe management module, that helps innovate, manage and store recipes with ease and then use them in production with a click where the manufacturers can review formula yield, and compare the actual yield vs. theoretical yield. This way, they get to know if a recipe is routinely requiring more material than expected, and can fix the problem of raw material shortages, delayed shipments, etc. caused due to varying yield.
– Operational costs
A food ERP software can help food manufacturers manage their fixed, variable, average as well as marginal costs. Besides, an ERP software for food industry can help them routinely develop forecasts and budgets, and predict how the different organizational decisions can influence the costs.
For example, using the ‘what-if analysis’ functionality, the food manufacturers can figure out how cost changes affect inventory valuation, pricing, and their business’ overall bottom line.
– Cost reduction through quality control
A food ERP software that comes with a robust quality control functionality can help big time with keeping the costs under check. It ensures your food manufacturing business has a set method of manufacturing to monitor quality control throughout the entire production cycle.
Creation of QC tests and well-defined inspection plans help ensure quality at all stages, which in turn reduces waste, makes valuable savings on costs, and helps you focus on tasks that improve profitability.
Just to put into perspective how much money you are losing due to manufacturing waste, a recent study found that the average manufacturer in the food industry throws away $59 million of waste each year! Surely a lot better could be done with that money!
Next, on to how ERP in food industry helps improve profits
– Business process standardization
An ERP software helps implement best practices across the organization, helping food manufacturers establish a standard way of doing things. The simplest of business processes, when standardized, translate into best business practices, delivering value in the form of waste elimination, reduction in errors, and eventually higher profits.
– Streamlined supply chain
We saw how having the right ERP in food industry ensures improved procurement, inventory management, demand forecasting, shipment, etc.- all the right ingredients for creating a robust supply chain. Further, with its bi-directional traceability, a food ERP software makes the supply chain all-the-more responsive, and its stakeholders, including key suppliers and the customers, happy and satisfied. The synergies between them translate into greater profitability for the business.
– Real-time visibility
By integrating all the business functions on a single platform, an ERP software allows access to consistent, accurate and real-time data to all and sundry. With a better insight into what is happening in the business at any given time, manufacturers can identify problems early, and take necessary preventive actions. These timely and informed decisions lay the foundation of a profitable business.
– Enhanced automation
Another way ERP software improve profitability is by introducing automation that aids in elimination of time-consuming manual tasks and errors, as well as speeding up of processes. Automation of processes such as procurement & management of raw materials, tracking of supplies, warehouse operations, maintenance and scheduling of the machines, and calculations of key business metrics lets the food business operate as a well-oiled machine, and end up with a much-improved bottom-line.
To sum up:
A good ERP software is without a shred of doubt an indispensable part of any food manufacturing business, as it helps the business reduce costs and increase its profitability manifolds. If yours is a food and beverage manufacturing organization that’s keen on exploring one such solution, your search ends at BatchMaster.
We have been serving the food and beverages manufacturing industry and its different micro-verticals with tailored and purpose-built software solutions successfully over the last 30-plus years. For more information or to set up a demo, connect with our experts today.